6000 urteko historia duen oinarrizko fabrikazio prozesua izanik, galdaketa teknologiak historia luzea ez ezik, aldi berean zientzia modernoan garatutako teknologia berriak, material berriak eta prozesu berriak xurgatu ditu denboran. Oinarrizko manufaktura industria hau aurrera eramateko erantzukizuna dugu. Hurrengo puntuak harea galdatzeko prozesuaren etorkizuneko garapen joerari buruz ditugun pentsamenduetako batzuk dira.
1 Galdaketa teknologia energia aurrezteko eta materiala aurrezteko bidean garatzen ari da
Galdaketa ekoizteko prozesuan, metala galdatzeko prozesuan energia kantitate handia kontsumitzen da. Aldi berean, harea galdatzeko prozesuan kontsumigarrien eskaera ere handia da. Hori dela eta, nola aurreztu energia eta materialak hobeto harea galdatzeko landareek duten arazo nagusia da. Normalean erabilitako neurriak honako hauek dira:
1) Harearen moldaketa aurreratua, core-making teknologia eta ekipamenduak hartzea. Hondarrezko galdaketa ekoizteko prozesuan, presio altuko, presio estatiko, injekzio presio eta airea zulatzeko ekipoak ahalik eta gehien erabili behar dira. Eta ahal den neurrian autogogortzeko harea, galdutako apar galdaketa, hutsean galdaketa eta galdaketa bereziak (esate baterako, inbertsio galdaketa, metal molde galdaketa) eta beste teknologia batzuk erabili.
2) Harea berreskuratzea eta berrerabiltzea. Burdinazkoak ez diren metalezko piezak, burdinazko galdaketak eta altzairuzko galdaketak egitean, hondarraren sinterizazio tenperaturaren arabera, mekanikoki birsortutako harea zaharra berreskuratzeko tasa% 90era irits daiteke. Horien artean, harea birziklatzearen eta hezeak birsortzearen arteko konbinazioa da metodo egokiena eta kostu eraginkorrena duena.
3) Itsasgarriak birziklatzea. Adibidez, galdaketa metodo lehorraz mozten bada eta itsasgarria hondarretan geratzen bada, prozesu egokiak itsasgarria berriro erabiltzea eragin dezake, horrela itsaskiaren kostua asko murriztuko da.
4) Moldeak eta moldeen materialak birsortzea.
2 Kutsadura gutxiago edo kutsadurarik ere ez
Hondarra galdatzeko burdinolak hondakin-ura, gas-hondakinak eta hauts ugari sortzen ditu ekoizpen-prozesuan. Hori dela eta, galdategia energia kontsumitzen duen etxe handia izateaz gain, kutsadura iturri handia da. Batez ere Txinan, galdategietan kutsadura beste herrialdeetan baino larriagoa da. Horien artean, harea galdatzeko lantegietatik isuritako hautsa, airea eta hondakin solidoak dira larrienak. Batez ere azken urteotan, Txinako ingurumena zaintzeko politikak gero eta zorrotzagoak dira, eta galdategiek kutsadura kontrolatzeko neurri eraginkorrak hartu behar izan dituzte. Harea galdatzeko ekoizpen berdea eta garbia lortzeko, aglutinatzaile inorganiko berdeak erabili behar dira ahal den neurrian edo aglutinatzaile gutxiago edo bat ere ez. Gaur egun esku hartzen duten harea galdaketa prozesuen artean, galdutako apar galdaketa, V prozesuaren galdaketa eta sodio silikato harea galdaketa ingurumenarekiko nahiko errespetagarriak dira. Galdutako aparraren galdaketa eta V prozesuaren galdaketa loteslerik behar ez duten harea lehorreko modelizazioa erabiltzen dutenez, sodio silikatozko harea galdatzeak lotesle organikoak erabiltzen ditu.
3 Fundizioen dimentsio eta geometria zehaztasun handiagoa
Hutsak galdatzeko zehaztasuna osatzeko prozesua garatzearekin batera, piezak osatzearen zehaztasun gemometikoa eta dimentsionala garatzen ari da forma gertu itxurako formatik sare formara arte, hau da, ia marjina osatzera. Galdaketa hutsaren eta beharrezko zatien arteko aldea gero eta txikiagoa da. Zenbait hutsune sortu ondoren, piezen azken forma eta tamainara hurbildu edo iritsi dira, eta ehotu ondoren zuzenean muntatu daitezke.
4 Akats gutxiago edo bat ere ez
Galdaketaren zimurtasunaren eta piezak osatzeko mailaren beste adierazle bat galdaketa-akatsen kopurua, tamaina eta kalteak dira. Lan beroa eta metal galdaketa prozesuak oso konplikatuak eta faktore ugarik eragiten dutenez, galdaketa akatsak saihesten dira. Hala ere, akats gutxi edo bat ere ez dira etorkizuneko joera. Hainbat neurri eraginkor daude:
1) Teknologia aurreratua hartzea aleazioaren egituraren dentsitatea handitzeko eta soinuen galdaketa lortzeko oinarriak finkatzeko.
2) Erabili galdaketa simulazioko softwarea aldez aurretik diseinu faseko galdaketa erreala simulatzeko. Simulazioaren emaitzen arabera, prozesuaren diseinua optimizatuta dago moldaketa puntualen eta moldeen proben arrakasta lortzeko.
3) Prozesuaren jarraipena indartu eta eragiketak zehatz-mehatz burutu zehaztutako eragiketa jarraibideen arabera.
4) Ekoizpen prozesuan saiakuntza ez suntsitzaileak indartu, estandarrak ez diren piezak denboran aurkitu eta dagozkien konponketa eta hobekuntza neurriak hartu.
5) Akatsen balio kritikoa zehaztea piezen segurtasuna eta fidagarritasuna ikertu eta ebaluatuz.
5 galdaketa ekoizpen arina.
Bidaiarien autoak, kamioiak eta bestelako garraio ekipamenduen ekoizpenean, piezen pisua minimizatzeko modua, piezen sendotasuna bermatuz gero eta joera nabariagoa da. Pisuaren murrizketa lortzeko bi alderdi nagusi daude. Bata lehengai arinak erabiltzea da, eta bestea piezen egitura diseinutik piezen pisua murriztea. Hondarrezko galdaketek egituraren diseinuan malgutasun handia dutelako eta metalezko material berri eta tradizional ugari ere badaude aukeran, harea galdaketak eginkizun izugarria izan dezake produkzio arinean.
6 Teknologia berrien aplikazioa, hala nola 3D inprimaketa moldeen fabrikazioan
3D inprimatzeko teknologiaren garapenarekin eta heldutasunarekin, galdaketa eremuan ere gero eta gehiago erabiltzen da. Moldeen garapen tradizionalarekin alderatuta, 3D inprimatzeko teknologiak azkar egin ditzake beharrezko moldeak kostu txikiagoarekin. Prototipoak egiteko teknologia azkarra denez, 3D inprimatzeak laginketa osoa eman diezaieke laginaren entseguaren ekoizpenean eta galdaketa sorta txikiko fasean.
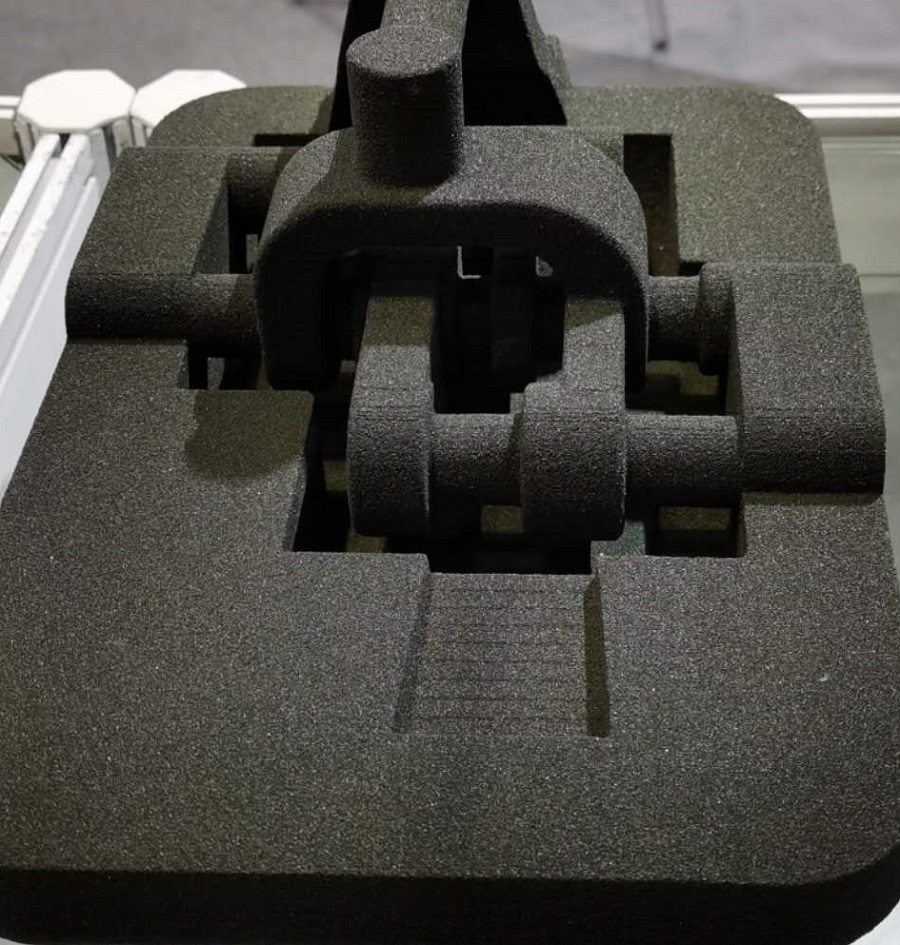
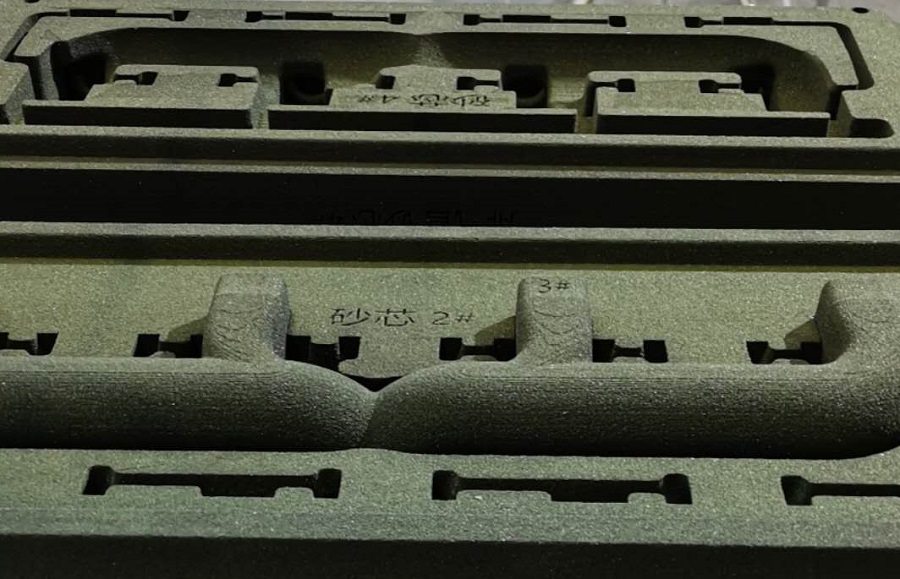
Mezuaren ordua: 2020ko abenduaren 25a